Connect with huge architecture firms and gain new business through Architizer’s community marketplace for building-products. Click here for more information.
We’re not judging you, honestly.
Everyone has bad habits, especially when it comes to business. We stick to routines that aren’t the most efficient, or getting so embedded in our work that we forget to consider alternative strategies that may be more effective. That is why — as painful as it might be — it is worth taking some time to pick apart common mistakes that can hold good companies back from making sales and achieving success.
Mark Mitchell of Whizard Strategy — a specialist consultant in sales and marketing for building material manufacturers — is a master at this. With fearless candor, Mitchell calls manufacturers out on their business errors and highlights focus areas that can help bring new customers in and keep existing ones happier. Using his viewpoints as a base, here are five classic habits that building-product manufacturers should aim to break in order to keep their company relevant to architects:
Bad habit 1: Forever expanding the product line.
Is it important to keep innovating and move with industry trends to remain a fresh choice for architects? Absolutely. But be wary of allowing your product range to spiral out of control over the years — it is possible to provide too much choice for designers, making it more difficult for them to decipher which of your products is truly an ideal fit for their project.
“If you have legacy products that are now a small part of your overall sales, cut them,” says Mitchell. It is vital to do regular reviews of every product in your range, calculating return on investment for each. If retiring the older, less profitable products gives your newer, higher-performing products the chance to take the spotlight, then be brave — architects will appreciate that your company moves with the times.
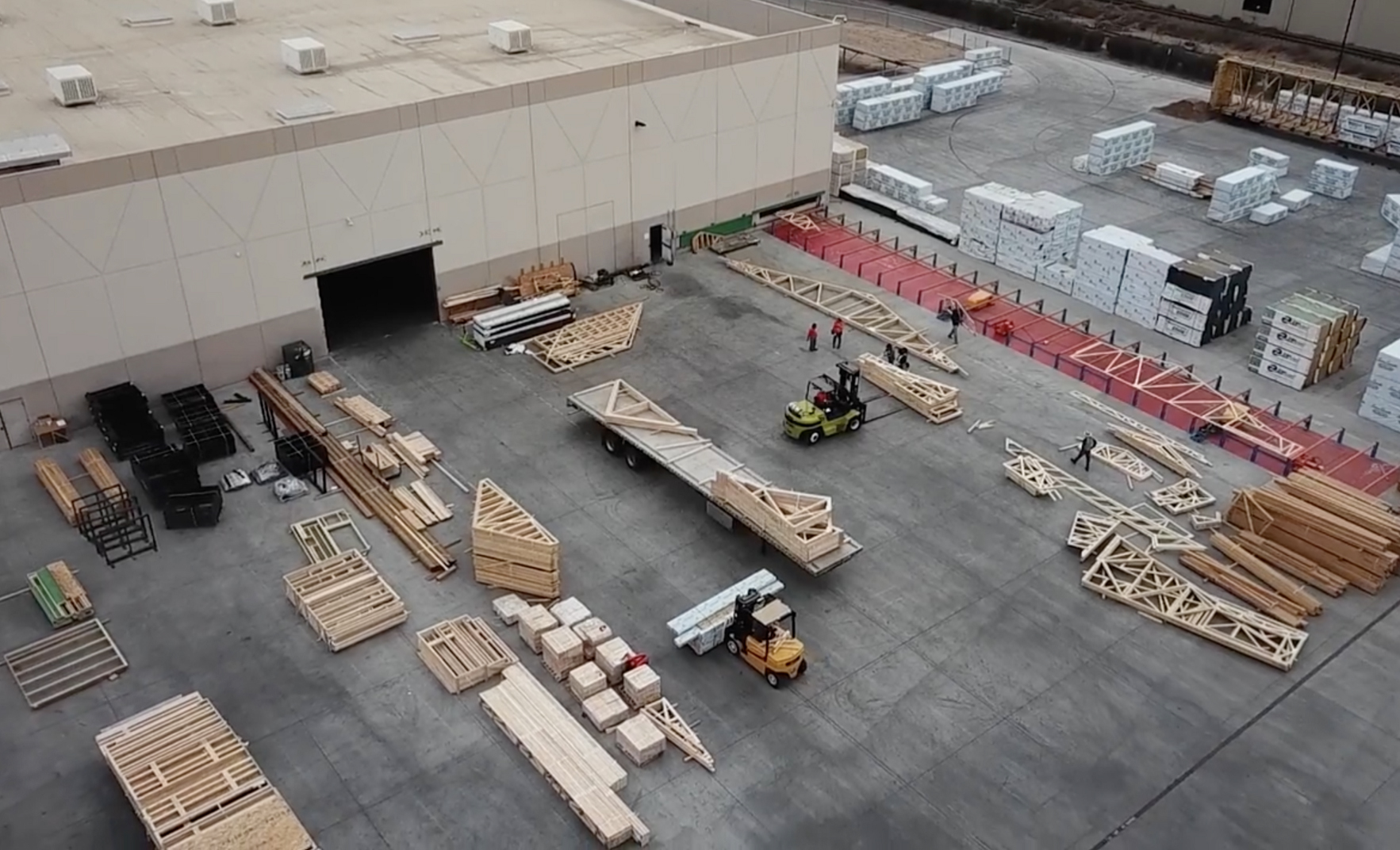
KATERRA factory; image via Medium
Bad habit 2: Thinking only about the present.
“Don’t stick your head in the sand and wait to become irrelevant,” urges Mitchell. His view is that, far too often, building-product manufacturers get stuck in their routines with sales and marketing. They rely too heavily on their existing list clients, not realizing that the construction landscape is shifting around them.
Mitchell’s go-to example of this is KATERRA, a pioneering company that creates pre-fabricated buildings from scratch, thereby expediting the construction process. KATERRA could be viewed as an existential threat to many building-product manufacturers, but if they learn everything they can about a company like this, they can establish how to either compete or collaborate with them. Always keep an eye on future trends, and consider how your company can be a key part of the “revolution”.
Bad habit 3: Being obsessed with competitors.
“Most building material manufacturers are too focused on their competition and not enough on their customers,” says Mitchell. Because of this, many manufacturers have a tendency to focus on lowering costs rather maximizing the quality of their product. The fear is that potential clients will always opt for the least expensive way to achieve their goal. But good value comes in many forms — not just a low cost per unit.
Improving customer service can lead manufacturers to win more commissions without having to lower any of their prices. The key is to focus on what your clients want, what their priorities are, what makes them tick. If you can help architects in their design challenges with great knowledge and guidance, they (and their client) will come to view you as indispensable. Suddenly, your competition becomes irrelevant.
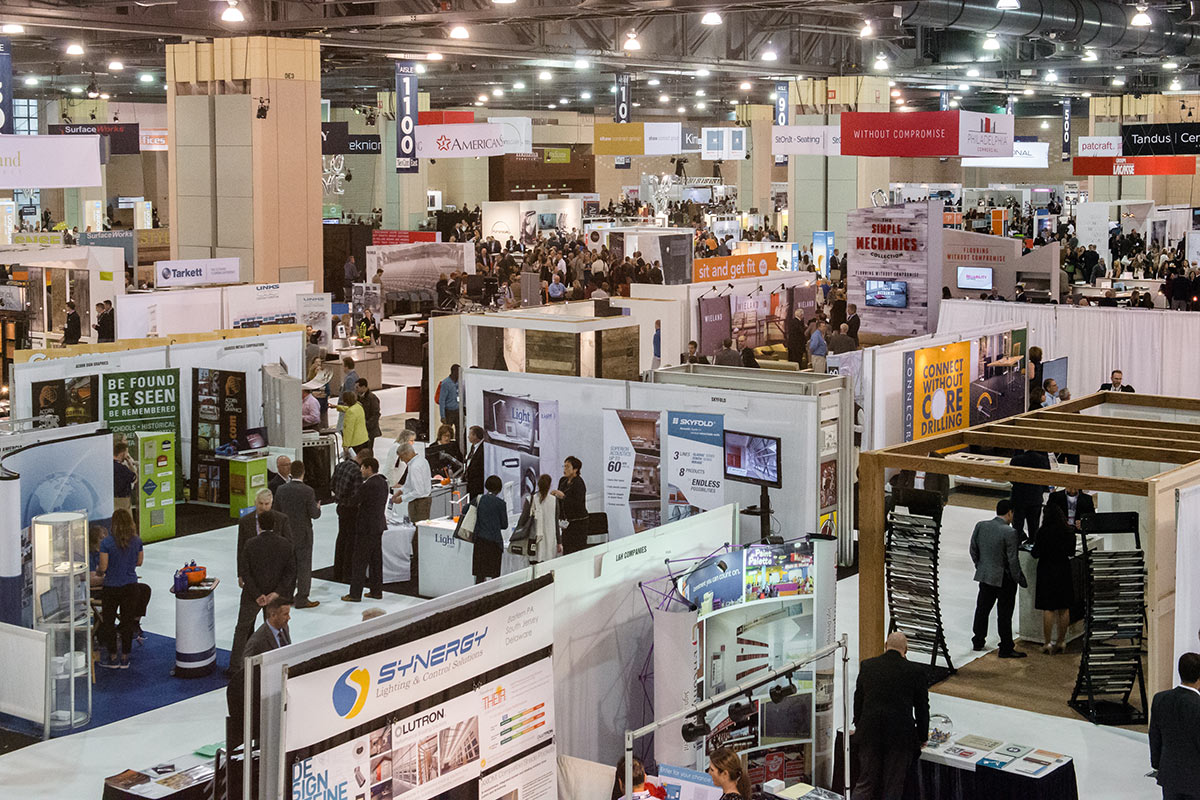
Neocon East; image via Neocon
Bad habit 4: Ignoring competitors.
As dangerous as obsessing over your competitors, discounting them can also cost you. Analyzing the approach of competitors can reveal not just what they are doing well (strategies you can copy) but also where they are weak (areas you can take advantage of). Mitchell does extensive “reconnaissance” on his client’s competitors.
“I don’t just check out competitors’ trade show exhibits,” said Mitchell. “I also study their website. I look at whether they are using social media and how. I analyze their SEO. Do they have a blog or engage in content marketing, and how good is it?” The key here is to be open minded. It is possible that your competitors are doing certain things better than you. Learn from them and you are more likely to overtake them.
Bad habit 5: Sticking with the status quo.
If you have a tried and tested formula that has resulted in sales then it may make sense to continue with that strategy. But all too often, manufacturers take this too far, avoiding the risks of new approaches and subsequently missing out on key opportunities in the industry.
“The building materials industry is ten years behind most other industries in marketing,” asserts Mitchell. He attributes this view to many things, from the industry’s lack of courage in leadership positions to manufacturer’s aversion to innovating online. Whatever your stance, it is clear that dynamism is vital to success in construction. Don’t be afraid to implement new sales and marketing strategies. Test, learn from and then optimize those strategies. In the end, brands that adapt will thrive.
Gain leads from major firms such as AECOM, HOK and OMA through Architizer’s community marketplace for building-products. Click here to sign up now.
Top image: iStock, credit: Palladadesign
The post 5 Bad Habits Costing You Sales With Architects appeared first on Journal.