Find the perfect glulam for your next project through Architizer’s new community marketplace for building-products: Click here for more information. Are you a glulam manufacturer looking to connect with architects? Click here.
In recent years, architects all over the globe have asserted glulam as a high-tech building material of the future — and one that we should all be paying a whole lot of attention to. As steel and concrete gradually fall to the wayside due to their steep environmental costs, timber architecture — in all shapes and sizes — is rising to exciting new heights.
According to Michael Green in his illuminating Ted Talk Why We Should Build Wooden Skyscrapers, “We’re at the beginning of a revolution, I hope, in the way we build, because this is the first new way to build a skyscraper in 100 years or more. But the challenge is changing society’s perception of possibility, and it’s a huge challenge. The engineering is, truthfully, the easy part of this.”
Glulam Systems
Glulam: Glued laminated timber is an incredibly versatile engineered wood that is frequently specified for its strength, beauty and reliability. The material is made up of several layers of structural timber that have been bonded together using adhesives in order to form a bigger, potentially enormous piece of wood. Building advancements using this material have drastically changed the scale of what is architecturally possible using timber.
Glulam is often advocated as a viable alternative to structural concrete and steel. When compared to concrete and steel, glulam can produce a lighter weight structure with a lesser carbon footprint that is much stronger, pound-for-pound. A variety of structural components can be formed using glulam including parallel beams, pre-cambered beams, sloped beams, curved beams, flight beams and trusses. The design possibilities are virtually limitless.
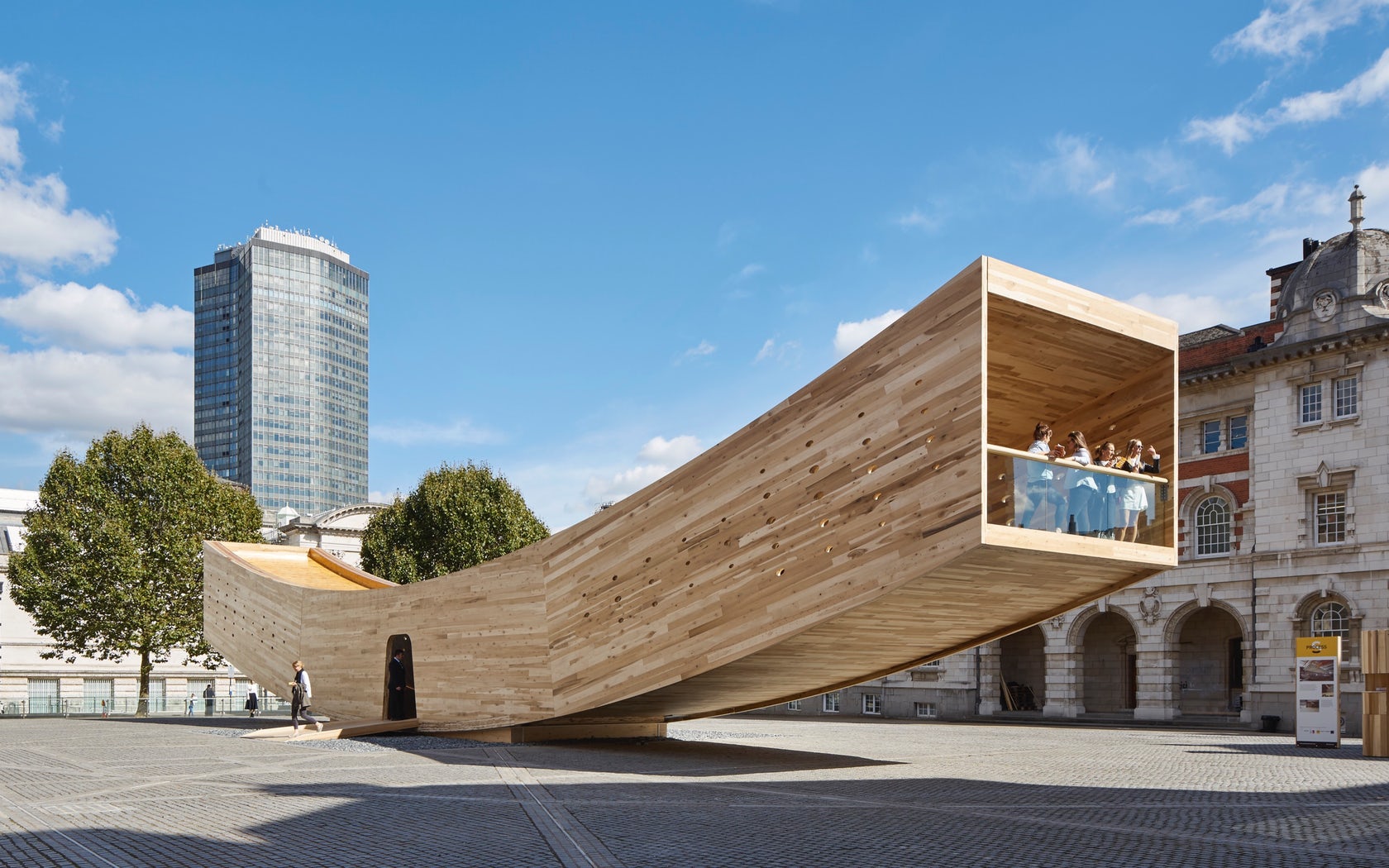
The Smile by Alison Brooks Architects Ltd was prefabricated as 12 industrial-sized tulipwood CLT panels by CLT pioneers, Züblin-Timber in Germany.
Cross Laminated Timber (CLT): CLT is another popular form of glued structural timber that has many of the same excellent capabilities. According to StructureCraft, “Cross Laminated timber (CLT) panels are formed by stacking and gluing together successive perpendicular layers of wood. The layered stacks are then pressed in large hydraulic or vacuum presses to form an interlocked panel.”
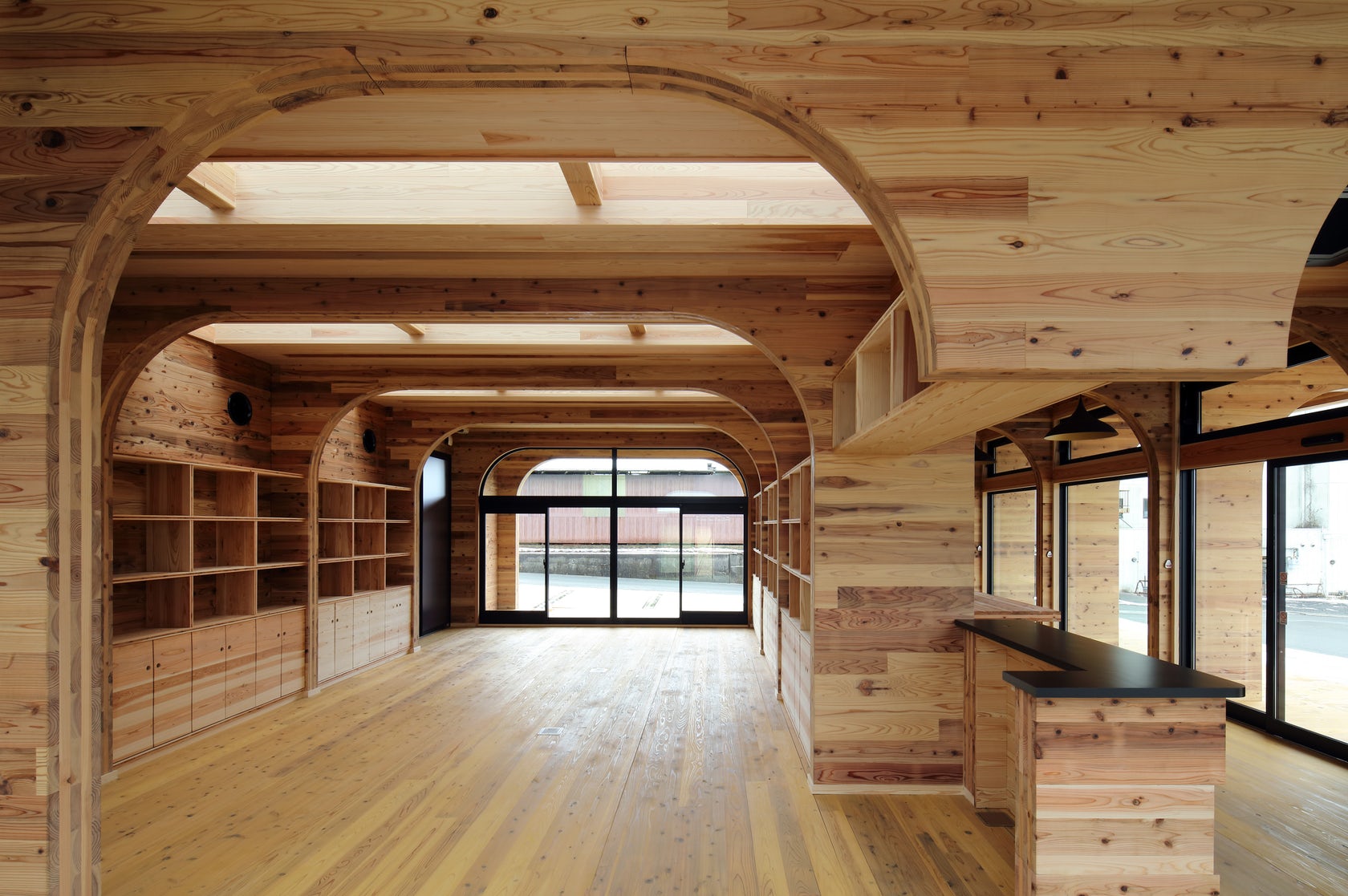
Santo CLT Office by Junichi Kato and Associates uses CLT as both the building’s structural and finishing material.
The number of layers in a panel typically range from three to seven, though they can vastly exceed this number. CLT panels can easily incorporate openings for windows and doors, as well as routings for electrical and mechanical systems, before they are shipped to site.
Aesthetics
Profiles: Using glulam, it is possible to achieve everything from simple arched forms to dramatic configurations with very tight radii. Curved glulam is manufactured by bending the laminated boards before they are bonded together with adhesives, clamped and cured.
Size: One of the greatest advantages of glulam is that it can be manufactured in a wide variety of sizes. Extremely wide beams can be manufactured by laying boards of different widths side-by-side, and reversing each layer so that there is an overlap and no straight-through vertical joint.
According to StructureCraft and the Structural Timber Association, the length of glulam panels are only limited by fabrication and shipping constraints. Theoretically, glulam panels can span any imaginable length and to date, roof areas exceeding 100,000 square-meters have been constructed using glulam framing.
Wood Grade: The ANSI A190.1 Standard — the APA’s standard for wood products — establishes nationally recognized requirements for the production and certification of structural glued laminated timber. These standards provide four appearance grades for glulam products: Framing, Industrial, Architectural and Premium.
Framing and Industrial grade appearance glulam are typically used in concealed areas that are not visible to the building’s public. When glulam is used as a façade material or exposed element, Architectural grade appearance glulam is highly recommended. Premium grade appearance glulam is typically only available on custom orders, and is used in instances where high traffic is expected. Premium grade glulam offers extremely high-quality and smoothly finished surfaces.
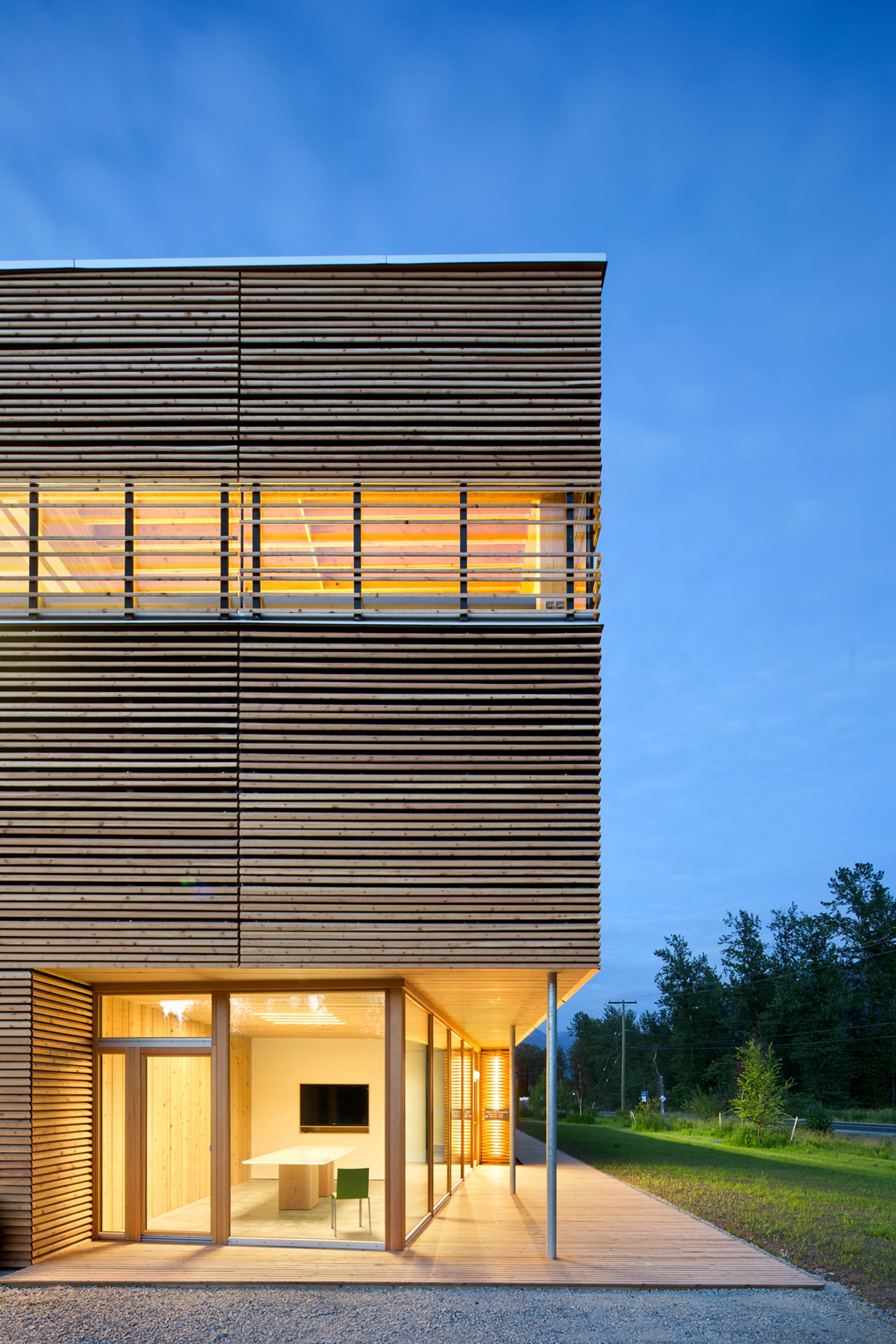
The main structure of the BC Passive House Factory by hemsworth architecture is Douglas fir glulam post and beam, with solid wood cross-laminated timber panel walls. All of these materials were manufactured in British Columbia by Structurlam.
Wood Species: A variety of wood species are appropriate for manufacturing glulam. Some of the most common types include SPF (Spruce-Pine-Fir), Douglas Fir, Larch and Alaskan Cedar. Less commonly, hardwoods such as Oak and Sweet Chestnut are also used. One bonus of glulam is that manufacturers can harness small pieces of wood that would have otherwise gone to waste.
Performance
Acoustic Performance: On its own, wood allows the majority of sound to pass through and does not absorb it particularly well. However, wood performs excellently when it is paired with a porous, sound-absorbing material. For more information, take a look at How to Specify: Acoustic Panels.
Applications: Common applications of glulam include floors, roofs, walls, shear walls and cores. Because of the material’s inherent load-bearing strength, glulam is appropriate in vertical and horizontal assembly applications.
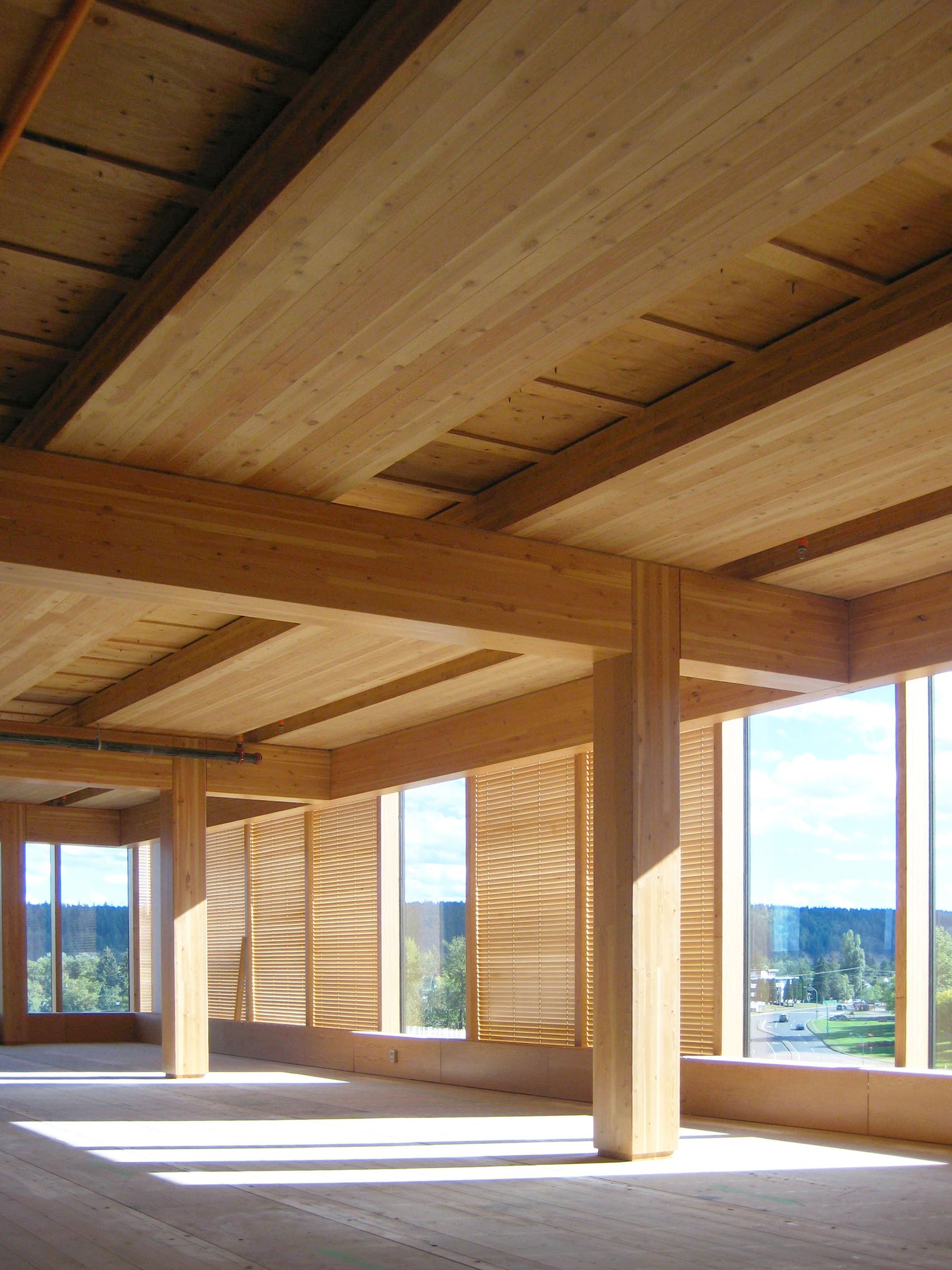
Wood Innovation and Design Center by MGA | Michael Green Architecture incorporates a simple, ‘dry’ structure of systems-integrated CLT floor panels, glulam columns and beams, and mass timber walls.
Construction Time: In comparison to concrete and steel structures, glulam projects can be installed in much shorter time periods since all of the materials arrive on-site prefabricated in a dry state. This also means that they require less storage and can be shipped just-in-time, which can prove very important in dense urban areas. On average, glulam can be installed three times faster than cast-in-place concrete.
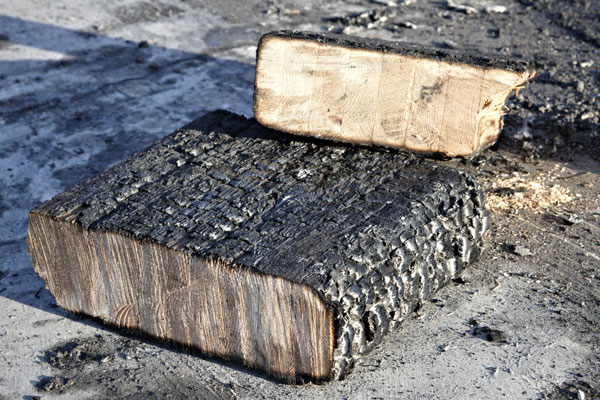
Charred glulam; Image via Rosboro
Fire Resistance: While timber frame structures have undergone ongoing scrutiny regarding fire resistance, rigorous testing has repeatedly confirmed that glulam provides excellent resistance to fire due to its charring characteristics. According to Wooderra, after 30 of fire exposure only around ¾-inch of glulam would be damaged whereas a steel structure would have collapsed under the same circumstances.
As noted in Popular Science, “Steel is vulnerable to melting in a blaze, twisting and contorting in the heat. Timber, on the other hand, will char on the outside, but flames will not penetrate its core. After the fire recedes, the wood beam will remain standing.”
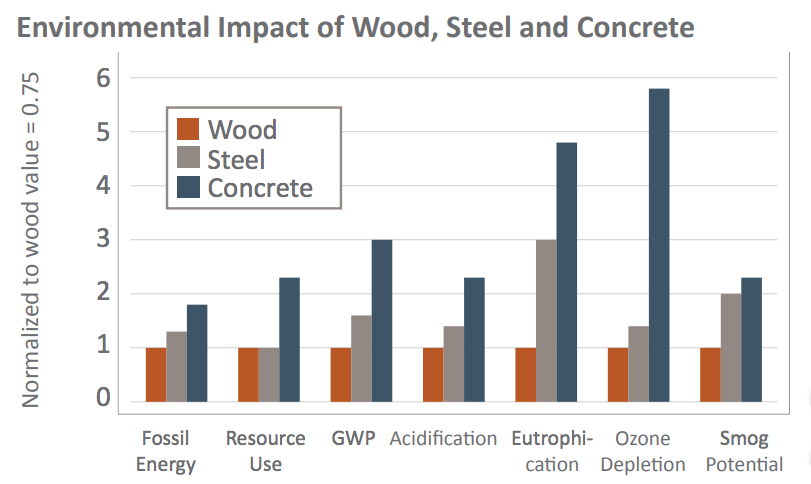
Graph depicting the environmental impact of wood, steel and concrete; Image via Structurlam by Dovetail Partners using the Athena Eco-Calculator (2014)
Sustainability: According to Michael Green in his Ted Talk Why We Should Build Wooden Skyscrapers, steel represents 3% of human-produced greenhouse gas emissions while concrete represents 5%, amounting to a grand total of 8% annually. Simultaneously, wood is the only material that architects can build with that is grown by the power of the sun.
Considering the environmental impacts of glulam as a building material typically follows two essential avenues: its capacity to reduce carbon emissions throughout production and remarkably, provide storage for carbon dioxide once buildings are completed and in use.
According to a 2014 study published in the Journal of Sustainable Forestry, as much as 31% of global carbon dioxide emissions could be avoided by building with wood instead of steel and concrete. In addition, timber frame buildings can actually sequester carbon dioxide, allowing them to serve as carbon sinks throughout their lifespan. Specifically, when used in buildings, 1 cubic-meter of wood can sequester 1 tonne of carbon-dioxide.
Thermal Properties: Glulam has remarkable thermal properties that help prevent thermal bridging and contribute to an efficient building envelope assembly. Additional insulation materials can also be paired with glulam; this will typically occur in the post-manufacturing stages of construction.
Case Studies
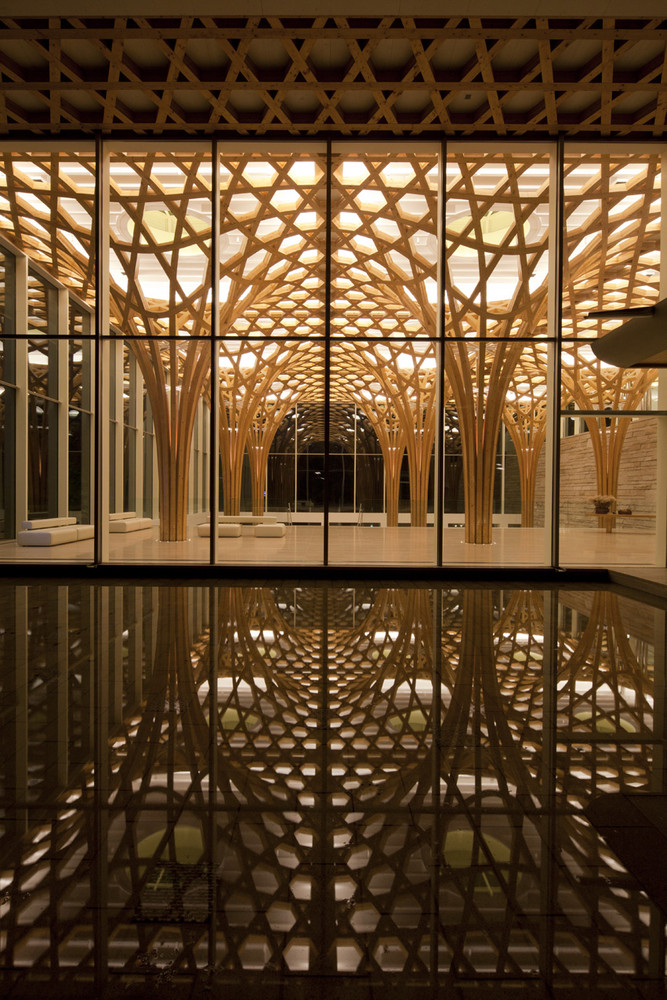
Nine Bridges Country Club by Shigeru Ban Architects; Glulam by Blumer-Lehmann; Photo via Shigeru Ban Architects
5 Gorgeous Glulam Structures by Shigeru Ban Architects
Shigeru Ban is a Pritzker Prize winning architect who has established himself as the undisputed master of unconventional materials. His completed projects — ranging from a museum built with reclaimed shipping containers, to a cathedral constructed of cardboard tubes and recycled plastic — appear less like a cohesive portfolio and more like a series of experiments, a continual search for newer, more sustainable ways of building. In recent years, this search has led Shigeru Ban to a material known as glued laminated timber. Through this miraculous material, Ban has been able to unite his passion for innovation with his eye for craftsmanship, producing intricate structures that push the boundaries of sustainable design.
Engineered Wood: Specifying Glulam for Every Architectural Typology
Glulam beams and columns come in many shapes and sizes. Because they are uniform, stable and predictable, engineering Glulam into a building is not just cost effective, but enables the creation of open spaces that would be difficult to achieve using regular wood frames. This collection of projects illustrates how this structural material can be utilized for a wide array of different building types, from homes and offices to churches and educational facilities.
Search for the perfect glulam through Architizer’s new community marketplace for building-products. Click here to sign up now. Are you a glulam manufacturer looking to connect with architects? Click here.
The post An Architect’s Guide To: Glulam appeared first on Journal.